Catering to the management and control needs of Delta Energy Storage System (ESS) Containers, our Delta Building Management and Control System (BMCS) can effectively integrate all equipment controls for diverse intra-container environmental variables, including air conditioning, lighting, fire protection, water detection, and others. There’s no need to further purchase extra, and often expensive, hardware control devices, thus saving time and money in system implementation. Remote monitoring and control can be easily achieved through a web interface for trouble-free management and control in real-time to ensure safe system operation.
Background
Delta’s Energy Storage System (ESS) Container is Delta’s own self-developed solution. It makes energy mobility easier with combining standardized modular energy storage battery units into a mobile container, which can be towed to a premise owner that experiences fluctuations in power loads, such as shopping malls, data centers, outdoor public events, or power failure rescue. It can be employed as an all-time economical solution ready for instant power provision, and is capable of dynamically scaling up or down capacity by adding or subtracting the number of operational battery units/containers. ESS Containers are often deployed in suburban areas where there may be no administrative staff on duty all the time. In this case, a complete and automated intra-container environment management and control system enables an authorized remote administrator to control, over a remote network connection, all environment variables such temperature, humidity, lighting, fire safety, and others, either for a single or multiple containers.
Challenges
There is high demand for ESS container durability in diverse fields. First, to maintain a decent battery life, the ambient temperature around the batteries should not be allowed to rise high. Further complicating the heat issue is hydrogen gas released as a by-product from the lead-acid batteries so often used in UPS and fire-safety backup power, which might exceed the designated safety standard and pose a danger of explosion. The ESS should be constantly monitored in an appropriately conditioned environment. Considering the highly mobile nature of the ESS container, an automated environment control system is a better option instead of a conventional human-controlled one. Subsystems in an ESS container, including ones for air-conditioning, lighting, fire protection, water detection and others, also requires a definitive solution to help manage the whole container effectively with a hands-on automation system for better control.
Delta Solutions:
● Rapid integration of different subsystems
Delta BMCS’s automation servers are capable of bringing a high degree of integration among diverse existing subsystems. Even a single controller already supports various standards and data exchange formats commonly used throughout the industry, and can effectively integrate all equipment controls for intra-container environment variables, including air conditioning, lighting, fire protection, and water detection. There is no need for the extra purchase of hardware control devices, saving time and money.
● Automated control saves management efforts
Automation servers are programmable controllers when coupled with specific I/O modules, and can utilize more data points as a means to integrate directly with more physical inputs and outputs for real-time monitoring and control. This is further strengthened with our advanced automated features such as alarm, scheduling, and historical trends, to save management time and effort.
● IP-based web interface for remote monitoring and control
An intuitive touch screen interface on site or at any remote computer’s web control interface lets an admin instantly monitor and control the status of a battery cabinet at any time, including its voltage, current loads, battery temperature, and more. With an energy storage system’s special requirements for ambient temperature, hydrogen gas concentration, and water, the automation server must automatically start/stop specific control equipment upon perceiving a critical anomaly and immediately adapt to environment changes. For example, if hydrogen detection shows an abnormally high concentration exceeding the set value configured on the automation server, the system will automatically start the exhaust fan and blower, while activating the alarm to send out an instant warning message to the admin(s). Or, if a critical anomaly is detected by the fire protection system, an alarm is triggered for instant warning.

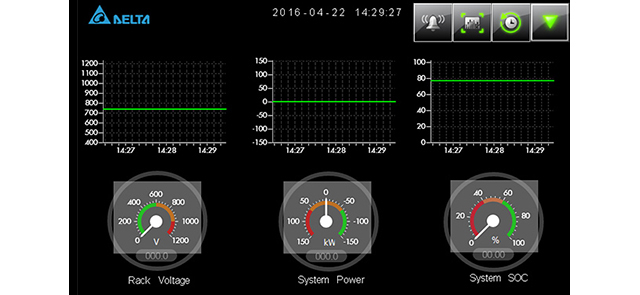