Traffic Safety for a Better Tomorrow –
Delta Tunnel Control Solution
Taiwan is a narrow and mountainous island, where highways, roads, and railways must go through tunnels. Currently there are more than 3000 tunnels with a total length of around 150km in Taiwan. In China, the traffic network has developed rapidly and it is now the country with the most tunnels in the world.
The fast growth and complexity of tunnels comes with increasing demands for tunnel control solutions. Delta has integrated its industrial automation products and solutions into a multi-layered decentralized tunnel control solution. This solution effectively masters and records traffic and facility operation in tunnels and ensures user and operator safety.
Delta Tunnel Control Solution
Application Background: In general, tunnels over 1km in length require a control system for ventilation, lighting, monitoring, traffic signs,fire alarms, closed-loop surveillance, emergency telephones and radio, and power control to assure safe and smooth traffic in the tunnels. The facility controllers connect to tunnel control centers for data collection, recording and analysis to form a complete tunnel solution.
For example: Taiwan's National Highway 3 tunnel control system can be divided into four layers: (Refer to Figure 1.)
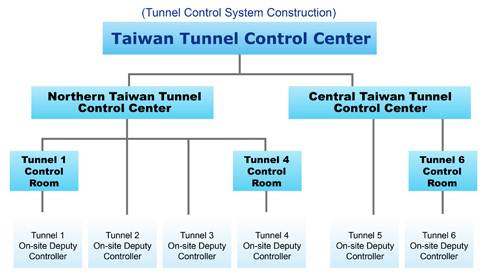
Figure 1: Virtual tunnel control architecture of National Highway 3 (Taiwan).
Main tunnel control center: Collects data from regional control centers to manage traffic in all tunnels along National Highway 3.
Regional control centers: Collect data from on-site controllers and tunnel control rooms within a certain region. In this example, the tunnels distributed along Nation Highway 3 are grouped into northern, central and southern regions.
Tunnel control rooms: Control tunnels of a certain length with constant heavy traffic On-site deputy controllers: Control on-site tunnel facilities.
The example above is a virtual structure. This solution is now widely applied to many tunnels in China.
The tunnel control system contains many electromechanical control devices in tunnels and control rooms/centers, so the system requires high-speed communication that guarantees mass data transportation. It also requires fault tolerance for high communications reliability.
If the tunnel control system adopts a programmable logic controller (PLC) as its control core, the PLC requires:
.Stability and reliability
.Data processing capability and fault protection
.Local processing capability for deputy controllers to avoid operation interference during a main controller breakdown
.Data exchange between deputy controllers
.Internet communication
.Fault tolerance and self-diagnosis functions
.Touch panel
Delta's Solution: Delta's tunnel solution can conduct real-time monitoring, rapid mass data transmission and it is easy to maintain. It adopts Delta's mid-ranged PLC AH500 Series for multi-layered decentralized tunnel controls, covering on-site deputy controllers and tunnel control rooms.
In each tunnel, Delta sets an AH500 Series every 400 meters to monitor on-site equipment and traffic signals through digital cables or RS232/480. The monitoring data is transferred to the main controller, which uses an AH500 Series with a human machine interface (HMI) in the control room through a fiber optic internet system composed of MODBUS TCP industrial Ethernet via Delta's DVS Series industrial Ethernet Switches. The data is analyzed and commands are sent out to deputy controllers for tunnel control. (Refer to Figure 2)
Figure 2: Delta's tunnel solution includes on-site equipment and controllers, control centers and network management.
.On-site equipment: Ventilation, lighting, traffic signals, traffic information panels, CO/VI sensor, lighting intensity detectors, wind speed/direction sensor, vehicle detectors and more.
.On-site deputy controller: Adopts Delta's AH500 Series mid-ranged PLCs that are connected to all control rooms and optic internet system composed of MODBUS TCP industrial Ethernet.
.Control Center: Includes dual hot standby server, communication computer and monitoring computer.
.Network management: Composed of on-line monitoring data center server and terminal computer to upload and release data on the website.